龙门刨床常用来加工大型工件的各种平面、斜面和槽,特别适宜于加工大型的、狭长的机械零件如机床的床身、导轨等,但对于中小型件、非连续面、端面如箱体等等,其加工效率就显得较低。目前我国六十到八十年代生产的各种龙门刨床数量相当巨大,在各机械加工厂占有较大比例,且能耗大、效率低,设备陈旧。同时,随着近年来产品结构的不断调整,各种中小型、非连续的加工零件也越来越多,单靠刨削加工已远远不能适应生产快速发展的需要。如何让这些当年价格不匪的老设备重新焕发生机,既能适应各种加工要求,又能节能降耗、有效提高加工效率呢?那就是经过机械、电气的综合技术改造,将单一的龙门刨床改为刨、铣两用机床。
在多年的龙门刨床改刨铣床的改造实践中,我们成功探索和总结出一套切实可行的改造方法,提高工作效率及企业的生产效益。以下是为某厂B2016A 龙门刨床(6米)的改造实例。
一、铣头的选择和安装:
选择铣头时,除能够满足加工要求,操作方便,安全可靠以及外观方面的要求外,应特别考虑到横梁的刚性,如果铣头较重而横梁承载能力较小,会出现铣头发抖而影响工件的加工精度和表面光洁度。与龙门铣相比,B2016A的横梁截面要小很多,也不宜选择较大较重的铣头。经过精选,我们在左垂刀架位置和左侧刀架位置各配置了一款性价比很高的龙门铣专用铣头,手柄调速,重量仅350KG,主轴电机7.5KW,满足一般铣削加工要求,最大可安装加工直径300mm的铣刀盘,套筒行程140mm,80-500mm/min共八种主轴速度,7:24的通用标准锥孔锥度,具可换性。
安装时,由于刀架溜板比铣头安装面小,我们增加了一块30mm厚的过渡连接板,打沉孔与溜板联接并定位,铣头初装好后,百分表打主轴旋转,用调整块调整铣头与工作台的垂直度,联接上紧后,垂直度误差不大于0.01/300mm,则工作台全宽误差不大于0. 05mm,满足一般加工精度要求,打定位销定位。
在各种改造中,曾有用户有角度旋转要求,即铣头可扳动±45°,实现的方法是,在过渡板上镗一孔,用原溜板上的法兰台阶定位旋转,在过渡板及溜板上部安装一套蜗杆配扇形蜗轮的传动机构,过渡板上有角度刻度线,并在需要的角度位置(如30°或45°)打定位孔。角度调整时,松开铣头固定螺丝,将拔插式的锥形定位销从0°定位孔拔出,扳动铣头到刻度指示的角度位置时,插入到该角度定位孔并锁紧即可。
二、工作台低速改造
工作台低速改造的方式很多,例如将原刨床减速箱更换为刨铣两用减速箱,或在主电机前端联轴器处加链轮或带轮,用一套减速机构拖动等方法。前者成本较高,后者若用链轮传动则刨铣转换不便,用皮带传动则力量不稳。实际改造中,我们采取在主电机尾端引出一根轴,增加拖动机构,并用牙嵌式电磁离合器来进行结合和分离主电机与拖动机构,来实现刨、铣的转换。60KW直流电机启动时,电磁离合器分离,工作台处于刨速度;变频电机启动时,电磁离合器结合,工作台处于铣削工作速度,主电机仅作为一个传动过渡轴使用,如下图一。
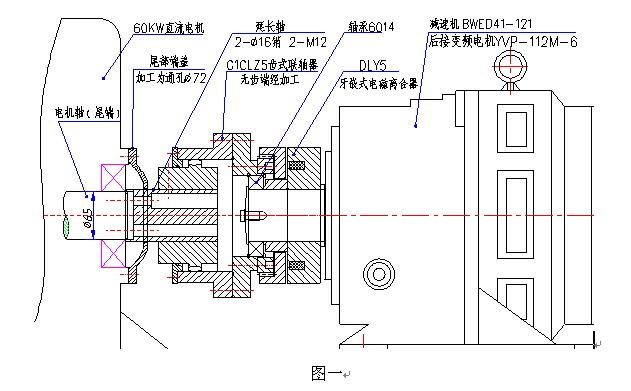
图一中,延长轴与尾部电机轴过渡配合安装,并用2-φ16直销加2-M12螺钉联接锁紧,在低速、小冲击的铣削时,2-φ16直销及2-M12螺钉完全可以承受拉动工作台所需的剪切力。延长轴锁紧后,其圆跳动不大于0.02mm。由于很多主电机使用年限较长,部分电机会有轴向2-5mm窜动,为此,我们选用能自动消除轴向窜动的内外齿联轴器,外齿固定于延长轴上,内齿在减速机轴上用轴承将轴向牢牢定位,保证在刨工作时不会使离合器意外结合。
拖动用的变频电机50Hz时转速1000r/min,经1:121的减速后,工作台最高速度为80/121=0.661 m/min, 因变频电机采用矢量变频器控制,调速范围可达1:20,则工作台的可调速度范围为0.03-0.66 m/min(高档)和0.015-0.033 m/min(低档),即工作台铣削进给速度范围为0.015-0.66 m/min,完全满足各种铣削速度要求。
2.2KW变频电机的额定输出力矩为9550×2.2/1000=21N.M,经1:121的减速机后力矩为21×121×75%=1905N.M(传动效率按75%),是原60KW直流电机输出力矩9550×60/1000=573N.M的3.3倍,因此,即使在变频电机处于低频而使输出力矩有所衰减的情况下也能保证有足够的拉力拖动工作台运动。
三、立铣头的横铣功能改造
立铣的横向铣削改造,如下图二
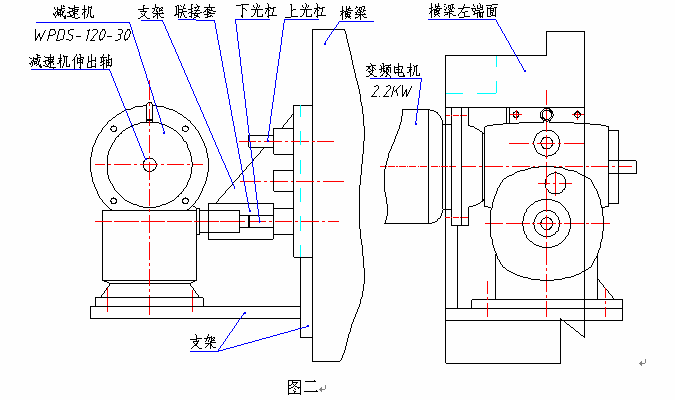
图二中,控制左溜板的下光杠要与横梁右端的传动机构脱开,手柄固定。减速机输入带伸出轴,便于手动调整。
2.2KW变频电机50Hz时的转速为1000r/min,通过1:30的蜗轮减速机减速后,下光杠转速1000/30=33 r/min,丝杆导程8×2=16mm,则横铣最快移动速度为33×16=533 mm/min,变频电机变速调节范围1:20,那么,横铣可调速度为27-533 mm/min,满足横向铣削速度要求。
因为横铣和工作台进给不会同时进行,横铣用变频电机与主拖动用变频电机同为6级2.2KW电机,因此,两个变频电机我们采用了同一个安川CIMR-G7A47P5矢量变频器来控制,只在悬挂按钮站上增加一个工作台与横铣的选择开关,这样就节省了一定的改造成本。
四、电气的综合改造
为达到和实现节能、可靠、减少故障、提高效率的目的,电气部分除增加变频控制及铣头电机控制部分外,我们对整个机床电气控制部分进行了如下改造:
一是取消原发电机组,仅保留直流电机,采用英国欧陆380A的590全数字直流调速装置驱动工作台60KW直流电机。原发电机组噪音大,起动电流大,对电网容量要求高,且空载电流达38-40安,在工作间隔时间(调整、装卸工件时间),这些电能被白白浪费。改用新型数字调速系统后,这个空载电流完全可以节省下来,且工作间隔时间越长,节电效果越明显,另外加上交磁发电机能耗以及多台电机能量传递损耗等,三项合计可平均每小时省电约12度。按两班工作制、0.65元/度计,每年仅省电就达0.65元/度×12度×16小时×24天×12月=3.6万元。同时也改善了工作环境,减低了噪声。
二是采用先进可靠的欧姆龙PLC检测各按钮、限位开关等信号,按照程序去控制各接触器及相关执行元件,有效地避免了故障点,提高了机床电气自动化程度,大大降低了机床的故障率和维修费用。
三是将原工作台换向采用的机械推压式改为无触点的电磁感应接近开关控制,使工作台运行更加稳定,更加安全可靠,并且接近开关更加经久耐用。
四是更换悬挂箱、电控柜及控制电缆,达到方便实用、运行可靠、无故障,提高效率的目的。
五是在工作台、横梁、刀架、侧刀架各轴加磁栅尺数显或数控的功能,使得机床更安全、稳定、可靠的提高工作效率。
|