本文介绍了早期的由发电机组拖动的龙门刨床或单臂刨床现存的问题,并简述了针对该种类型的刨床改造方式:采用全数字直流调速装置组合先进的PLC控制方式,着重强调了改造后的节能降耗所带来的经济效益以及改造后的其它特点。
一、龙门刨床电气改造的必要性
随着社会的进步,科技的发展,产于上个世纪七、八十年代的龙门刨床的电器控制线路已经十分落后,而且老化严重,故障频繁,维修非常困难,费时费力,效率低,能耗大,同时噪音也很大,污染严重。经过多年的时间经验,我们对老式龙门刨床的电气控制线路进行了彻底的技术改造,将发电机组、交磁扩大机控制的龙门刨床改造成为全数字智能化的电气控制系统。
上个世纪七、八十年代的龙门刨床工作台一般是由一台60KW直流电机拖动。该直流电机参数为:60KW,220V,305A,1000RPM,励磁为220V,4.11A。该直流电机电源采用电动机-直流发电机组和交磁扩大机提供(简称K-F-D系统),采用调直流发电机的励磁电流方式来改变直流电动机的电枢电压,从而达到调速的目的。原来整个电气控制系统比较复杂,使用电器元件也比较多,加之使用时间长,故障频繁。我公司综合以往改造经验,B2010A、B2012A、B2012Q、 B2151、B2152、B2016A、BJ2020、B20125Q等10余种型号的龙门刨床及单臂刨床都很适合全数字智能化控制的电气系统改造。
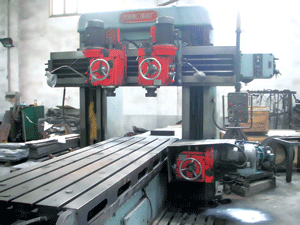
二、早期龙门刨床的特点:
1、刨床的工作台驱动是由交流电动机、直流发电机、直流电动机及交磁扩大机组成。K-F-D控制系统的主要缺点是:起动电流大,对电网容量要求高,机械传动能耗大,传输效率低。
各电机基本参数见下表:
2、改造前的龙门刨床电控系统存在的问题及缺点:
⑴ 设备使用时间长达数十年,电器元件严重老化,故障率频繁,维修费用高,已不能满足目前生产加工的需要;
⑵ 由于采用的是交直流电动机组,其效率只有0.5~0.68,并且能耗高;
⑶主传动及控制部分中间环节较多,不但增加了维护工作量,也使整个系统可靠性大大降低。
⑷工作台换向及减速靠机械式限位开关实现,减速及换向时撞击声音大,且整个电控系统附带有各种电阻、继电器多,故障点多,低速时速度不稳,换向不稳定,常会出现爬行、越位等故障;
⑹ 工作台调速范围小,精度(D≤30),加工工件的表面质量差;
⑺占地面积大,噪音高。
三、龙门刨床改造方式及改造后的特点:
1 .龙门刨工作台直流电机调速系统的改造:
改造后的龙门刨床工作台直流电机采用英国欧陆公司生产的590+/380A直流调速装置驱动,完全取代直流发电机组和交磁扩大机,实现了工作台的无级调速、自动减速、换向以及撞到极限限位后停车等动作。欧陆590+是具有较高水平的全微机化工业直流电机调速驱动器,输出电流范围在15A~2400A,该产品还具有控制、监控、保护和串行通讯的功能。
590+直流调速装置还有一系列可供用户随意设定的参数,这些参数有些来自外部,如速度给定、转矩给定、速度反馈以及电机的各种特性参数等,同时配备I/O接口,以及P3串行通讯接口,可以方便的与上位机联接通讯,以满足各种参数设置以及与其他装置通讯的需要。
2.用PLC实现龙门刨床的其他电器动作的自动控制:完成龙门刨床自动进刀、抬刀、落刀、横梁升降、横梁夹紧放松、各刀架快速移动以及工作台的加速、减速、换向等各种动作的正常运转。
3. 工作台行程限位开关更换为电磁感应的接近开关:性能更稳定,响应时间快,而且使用寿命更比原来的行程开关更长久。
4.在直流电机尾端加装测速发电机后:实现闭环控制,提高控制及定位精度。
5、使用效率:
由欧陆 590+和PLC相互配合进行改造后的龙门刨床控制系统最低速度可达5rpm,最高为1500rpm,从起步到全速只需8秒时间,甚至更短时间。从全速到减速换向,可在12秒时间内完成,且换向平稳无冲击,不会发生振荡、爬行、越位等现象,同时可以恒转矩切削,因而大大提高加工精度及效率。通过悬挂按钮箱能完成系统的启动、停止、自动等功能。加工长度范围由悬挂按钮站和工作台上的可以滑动的挡铁完成行程设置,并可以通过PLC的记忆功能来保存,电气柜上有各种报警指示,几乎可以实现无故障、免维护运行。
四、龙门刨床电气改造后经济效益分析
使用欧陆 590+直流调速装置和 PLC结合控制后,节能效果十分明显,改造周期短。因此,将先进的直流调速装置应用到龙门刨床的工作台调速中,无疑是一种很大的技术革新,可以带来较大的经济效益。
以下是我公司对某厂B220型龙门刨床改造前后的测试实例:
其主传动部分(工作台)采用直流发电机组拖动直流电动机,功率60KW,是主要能耗。其余功耗如横梁升降和刀架的进给等较小可忽略不计。经改造后,电费成本、工艺性能、工作环境及电网干扰等均得到显著改善。
1、 测试参数:
有功功率、三相电流、三相电压、功率因素、噪音强度、工作台的进给速度等
2、 改造前后测试相关参数:
3、 结论分析:
⑴技术数据
⑵老式控制系统与新式控制系统的效果对比见下表:
⑶所产生效益
①直接经济效益
原发电机组在多年生产、制造及用户使用中测定,其起动电流大,对电网容量要求高,且空载电流达80-100安,在工作间隔时间(调整、装卸工件时间),这些电能被白白浪费。改用新型数字调速系统后,这个空载电流完全可以节省下来,且工作间隔时间越长节电效果越明显。按计算,节约功率为△P:
U2=380V;△I取其空载电流中间值
90A;COSΦ取0.40
则△P=1.732×380×90×0.4=24kW
每小时节电24度,按每天工作间隔时间三小时、全年按310天计算:
年节电:W=24×3×310=22320kWh
拆除交磁发电机后,每小时可节约电能约3kW,按每天两班制计算:
年节电:W=3×16×310=14880 kWh
另外,采用新型数字调速系统,可以省去了由多台电机之间电能传递而造成的效率损失,其数值为所需加工零件电能的6-10%,按一般性加工时,每天省去的传动效率损耗为80度,全年节电即为24800度。
以上三项合计,全年节电可达6万多度,若每度按0.6元计算,全年节电约为4万余元。
②提高了机床的电气自动化程度,大大降低了机床的故障率和维修费用,年节约成本约1万余元.
③占地面积小,无噪声。除此外,拆除后的发电机组还可以再利用,创造更多的经济价值。
4.改造后的龙门刨控制系统的特点:
⑴ 该数字直流传动装置能耗低,效率高。工作间隔无损耗,大大节约电能,其效率可达到0.95以上,而直流发电机组只有0.7左右;
⑵起动电流小(起动电流I≤1.5Ie),对电网的冲击小;
⑶调速性能高。590+是一种高精度传动装置,以其自身的优点使整个主传动控制系统的精度、调速范围、快速性能有了很大的改善,提高了加工能力及其加工质量;
⑷ 结构简单,可靠性高。与交磁扩大机组相比,全数字可逆直流调速装置可减少70KW直流发电机一台,55 KW交流电动机一台,交磁放大机一套,同时大大减少了占地面积,使控制系统结构简单、体积缩小;
⑸ 其它动作均由PLC实现,电器元件少,简单直观。用可编程控制器取代繁杂的交直流继电器控制,大大提高了系统的可靠性,同时维护也十分方便,减少运行成本;
⑹ 装机水平高,具有完善的保护功能。系统具有良好的保护和监控功能,PLC有自身的输入/输出监控指示灯,而全数字直流调速装置则更有良好的保护监控功能,具有故障存储记忆,自适应参数优化等多种功能;
⑻ 改造后,由于取掉了交流机组,因而可无噪音运行。
结论:早期由发电机组拖动的龙门刨床和单臂刨床都很适合上述电气改造方式。改造后,不仅能耗大大降低,使用效率也得到很大提高。用户仅需要投资几万元,经过一两年的时间就可以收回成本。 |